Şişirme Extruder Prosesleri
Plastik enjeksiyon yöntemi geniş bir aralıktaki plastik tüketim malzemelerinin üretilmesindeki ekonomik ve popüler yöntemlerden birisidir. Bu yöntemle araç panelleri, bilgisayar parçaları, ev eşyaları gibi ürünler üretilebilmektedir. Bu ürünler plastik enjeksiyon yöntemi kullanılarak farklı ölçülerde ve çeşitli ihtiyaçları karşılamak için seri üretim yoluyla üretilebilmektedirler.
Bu yöntemle termoplastikler, termosetler ve bazı elastomerler kullanılarak imalat yapılabilmektedir. Yöntem plastik ham malzemenin sıcaklık yardımı ile eritilmesinin ardından bir kalıbın içine basılarak istenilen şekle getirilmesi prensibine dayanır. Ham malzeme istenilen şekle gelirken kalıp içerisinde soğur ve parça kalıptan çıkarılır. Teknolojik gelişmeler ile birlikte, bu yöntemle 15 gramdan yaklaşık 23 kilograma kadar parçalar imal edilebilmektedir.
Ekstrüzyon Şişirme Makinesi Prosesi;
1. Ekstrüzyon Şişirme (Sürekli, Akümülatif ve Ko-Ekstruzyon)
2. Stretch Şişirme
3. Enjeksiyon Şişirme
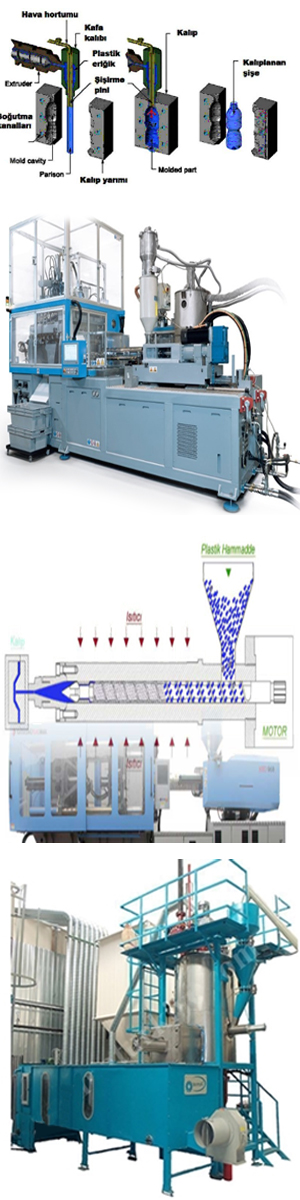
4. Enjeksiyon Stretch Şişirme
Bunun dışında dünya şişirme teknolojilerinde yerine alan dalma metodu (dip blow molding) ve rotasyon metodu da (molding with rotation) bulunmaktadır. Yukarıda söz konusu olan uygulamalarını bulabileceğimiz Ekstrüzyon şişirme teknolojisi, şişirme dünyasında en çok kullanılan metotların başında gelmektedir.
Genel Şişirme Yöntemleri ve İşlem Sırası; Şişirme Prosesi şişirme mantığı bakımından birbirinden farklı iki alt gruba ayrılmaktadır, ekstrüzyon şişirme ve streç şişirme işlemi. Kısaca açıklamak gerekirse; Streç şişirme prosesinde daha önce enjeksiyon makinesi ile kalıplanmış preformlar tekrar ısıtılarak bir şişirme çubuğu yardımıyla gerilir ve basınçlı hava ile bu gerilmiş preformlar şişirilerek tekrar kalıplanmış olur.
Yukarda sayılan basamakların dışında ürünü etiketlemek veya sızıntı testi yapmak için opsiyonel ekipmanları makineye bağlayarak prosesin basamaklarını arttırmak mümkündür. Çok büyük hacimlerdeki konteynerler için parisonun açıta ki ucunu sağlam bir şekilde birleştirmek için kaynak cihazları da prosese dâhil edilmektedir. Bir ekstrüzyon şişirme makinesini incelersek aşağıda anlatıldığı gibi birkaç alt sisteme ayrıldığını görürüz;
Genel Parçalar;
Enjeksiyon Ünitesi, Kalıplama Ünitesi, Mengene Ünitesi.
Çalışma Prensibi;
Hammadde kurutma ünitesinde proseste kullanılacak hammaddenin özelliklerine göre uygun sıcaklıkta yeterli süre bekletilir.
Plastikleştirme Aşaması;
Kurutulmuş hammadde besleyicinin kapağı açılarak sonsuz vida yardımıyla ısıtıcı birimlere doğru itilir. Burada farklı sıcaklıklardaki ısıtıcılardan geçerek eriyen malzeme enjekte memesine doğru hareket eder. Isıtıcıların sıcaklıkları kullanılacak hammaddenin erime sıcaklığı, akışkanlık değeri, parça cidar alınlığı gibi faktörler göz önüne alınarak belirlenir. Genel Şişirme Yöntemleri ve İşlem Sırası; Şişirme prosesi şişirme mantığı bakımından birbirinden farklı iki alt gruba ayrılmaktadır, ekstrüzyon şişirme ve streç şişirme işlemi. Kısaca açıklamak gerekirse; Streç şişirme prosesinde daha önce enjeksiyon makinesi ile kalıplanmış preformlar tekrar ısıtılarak bir şişirme çubuğu yardımıyla gerilir ve basınçlı hava ile bu gerilmiş preformlar şişirilerek tekrar kalıplanmış olur.
Ekstrüzyon Şişirme Prosesinin Temel Basamakları Aşağıda Sıralandığı Gibidir;
1. Termoplastik hammaddenin bir ekstrüderde plastikleştirilmesi ve hazırlanması,
2. Dikey bir akış ile erimiş plastiğin yönlendirilmesi,
3. Erimiş hammaddenin parison denilen akışkan hortum haline getirilip kafadan dışarı akıtılması,
4. Parison aktığı kafaya, sadece kafa, ekstürüzyon kafası, şişirme kafası ve parison kafası da denilmektedir,
5. Kafadan akan parisonun bir kalıbın arasında mengene yardımı ile kıstırılması,
6. Şişirme pinleri ya da şişirme iğneleri (ya da siboblarının) kapalı olan kalıbın içine girmesi,
7. Soğutma suyuyla soğutulmuş kalıp duvarlarının arasındaki parisonun şişirme pinleri aracılığı ile basınçlı hava ile şişirilmesi ve şişirme işleminin sonunda boğaz çapağından arındırılması,
8. Kalıbın açılarak şişirilmiş ürünün şişirme pininde asılı kalması,
9. Şişirilmiş ürünün kenar bölgelerindeki çapaklarından arındırılması.
Eriyik Basınç Sensörü Nedir ?
Eriyik Basınç Sensörü, Plastik hammaddelerin yüksek sıcaklıklara ulaşabildiği işlemlerde erimiş sıvıların basıncını ve sıcaklığını (isteğe bağlı) ölçmek için kullanılan ensturman dır.
Eriyik Basınç Sensörü Neden Gerekli ?
Neredeyse tüm ekstruderler en az bir erime basıncı dönüştürücüsü kullanmaktadır, çünkü erime basıncı / sıcaklık kontrolünün ekstruzyon işleminin kalitesini arttırması istenmektedir.
* Emniyet,
* Ekipman Koruması,
* Daha Yüksek Verimlilik,
* Daha Yüksek Ürün Kalitesi.
Şişirme Extruder Prosesleri için Eriyik Basınç Sensörü Uygulamaları;
Kalıpta Eriyik Basınç Sensörü / Eriyik Basınç Kontrolü Uygulaması
Amaç;
* Erime basıncı, akış stabilitesini kontrol etmek,
* Üretim için gerekli Basıncın oluşmasını sağlamak,
* Üretim için gerekli reçetelerin oluşturulması,
* Plastik hammaddenin Değerlendirmesini yapılması,
* Basıncı Kontrol etme,
* Vida üzerinde gereğinden fazla Basıncın oluşmasını önleme,
* Vida aşınmasını koruma altına alma.