Tekstil Üretim Extruder Prosesleri
Mikrolif teriminin tanımlanmasında genellikle lif çapı veya dtex veya denye olarak filament numarası göz önüne alınmaktadır. Buna göre, 0,1-1,0 dtex aralığındaki lifler mikrolif olarak tanımlanmaktadır [1, 2]. 0,1 dtex değerinden daha ince lifler ise, süper mikrolif olarak adlandırılmaktadır. Mikrolif yünden 40 kez, pamuktan 30 kez, ipekten 10 kez daha incedir, Sürekli filament şeklinde üretim, Direkt lif çekim yöntemi (konvansiyonel yöntem) 0,1-1,0 dtex aralığındaki herhangi insan yapımı lif mikrolif olarak tanımlanmaktadır. En çok üretilen insan yapımı mikrolifler polyester, naylon, polipropilen, akrilik ve viskozdan oluşmaktadır, Mikrolifler kullanım amacına bağlı olarak kesiksiz filament veya kesikli stapel şeklinde üretilmektedir. Mikrolifler, konvansiyonel lifler ile karşılaştırıldıklarında kumaşlara lüks görünüm, iyileştirilmiş fiziksel ve tutum özellikleri ve yüksek seviyede giyim konforu sağlamaktadır.
Bu nedenle, son yıllarda mikroliflere karşı artan bir eğilim bulunmaktadır. Mikrolifler yüksek kalitedeki giysiler, abiye kıyafetler, spor giyim, ev tekstilleri, endüstriyel ürünler gibi birçok alanda yaygın olarak kullanılmaktadır. Mikrolif teriminin tanımlanmasında genellikle lif çapı veya dtex veya denye olarak filament numarası göz önüne alınmaktadır. Buna göre, 0,1-1,0 dtex aralığındaki lifler mikrolif olarak tanımlanmaktadır. 0,1 dtex değerinden daha ince lifler ise, süper mikrolif olarak adlandırılmaktadır. Mikrolif yünden 40 kez, pamuktan 30 kez, ipekten 10 kez daha incedir.
Mikrolif üretimi sürekli filament ve kesikli lif (stapel) olmak üzere 2'ye ayrılmaktadır. Sürekli filament üretim yöntemi direkt lif çekim (konvansiyonel lif çekme) ve bikomponent çekim yöntemi olmak üzere 2 şekilde gerçekleştirilmektedir. Konvansiyonel lif çekiminde bilindiği gibi, polimer ya gaz (çoğu kez bu gaz havadır) ya da solüsyon içine basılmakta ve daha sonra da çekilmektedir. Polimerler düzelerden geçirilmeden önce ya eriyik haline ya da çözeltileri haline getirilmektedir. Polimerlerin eritilerek düzelere gönderilmesi eriyikten lif çekme, polimer çözeltisinin kullanılması ise çözeltiden lif çekme olarak tanımlanmaktadır.
Mikrolif üretiminde genellikle eriyikten lif bu nedenle, çekme yöntemi kullanılmaktadır. Polimer viskozitesinin uygun hale getirilmesi (yüksek çekim sıcaklığı viskoziteyi azaltmaktadır). Düze tasarımının uygun hale getirilmesi (düze deliklerinin homojen soğutma verecek şekilde düzenlenmesi). Düze altındaki ortam sıcaklığının uygun hale getirilmesi (soğutma hızının kontrol edilmesi). Filamentlerin bir araya getirilmesinin uygun şekilde yapılması (düzeye en yakın yerde bir araya getirme). Lif çekiminin uygun hale getirilmesi (eğirme geriliminin kontrol edilmesi). Düşük hızda çekim (düzgün polimer iletimi).
Genel Parçalar;
Ekstrüder, ölçüm pompaları, kalıp montajı, ağ oluşumu ve sarım sistemi.

Çalışma Prensibi;
Granüller veya toz plastiklerden şekillendirilmiş nesneler üretilmesi için çok çeşitli metotlar geliştirilmiştir.
Eriyik Basınç Sensörü Nedir ?
Eriyik Basınç Sensörü, Plastik hammaddelerin yüksek sıcaklıklara ulaşabildiği işlemlerde erimiş sıvıların basıncını ve sıcaklığını (isteğe bağlı) ölçmek için kullanılan ensturman dır.
Eriyik Basınç Sensörü Neden Gerekli ?
Neredeyse tüm ekstruderler en az bir erime basıncı dönüştürücüsü kullanmaktadır, çünkü erime basıncı / sıcaklık kontrolünün ekstruzyon işleminin kalitesini arttırması istenmektedir.
* Emniyet,
* Ekipman Koruması,
* Daha Yüksek Verimlilik,
* Daha Yüksek Ürün Kalitesi.
Tekstil Üretim Extruder Prosesleri için Eriyik Basınç Sensörü Uygulamaları;
Kalıpta Eriyik Basınç Sensörü / Eriyik Basınç Kontrolü Uygulaması
Filtre Öncesi Eriyik Basınç Sensörü / Eriyik Basınç Kontrolü Uygulaması
Filtre Sonrası Eriyik Basınç Sensörü / Eriyik Basınç Kontrolü Uygulaması
Melt-Dişli Pompa Öncesi Eriyik Basınç / Eriyik Basınç Kontrolü Sensörü Uygualaması
Melt-Dişli Pompa Sonrası Eriyik Basınç Sensörü / Eriyik Basınç Kontrolü Uygualaması
Cips Kesiciler Eriyik Basınç Sensörü / Eriyik Basınç Kontrolü Uygualaması
Amaç:
*Erime basıncı, akış stabilitesini kontrol etmek,
*Üretim için gerekli Basıncın oluşmasını sağlamak,
*Filtre değiştiriciyi tıkayabilecek ve kalıpta basınç düşmesine neden olabilecek muhtemel kirlenmenin izlenmesi ve sonuç olarak tıkalı filtrelerin değişiminin yapılması gerektiği tespit etmek, (bu nedenle basınç ekran değiştiriciden önce ve sonra ölçülür)
*Dişli pompa, kalıba sabit akış hızı vermek için kullanılır: akış ölçülen basınç değerine bağlı olarak ayarlanır (basınç değeri, vida hızı ayarı için sürücüye geri bildirim vermek için kullanılır)
*Üretim için gerekli reçetelerin oluşturulması,
*Plastik hammaddenin Değerlendirmesini yapılması,
*Basıncı Kontrol etme,
*Vida üzerinde gereğinden fazla Basıncın oluşmasını önleme,
*Vida aşınmasını koruma altına alma.
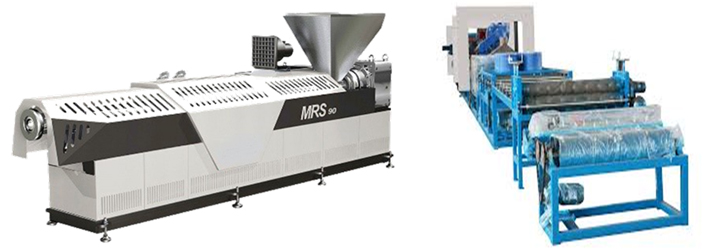
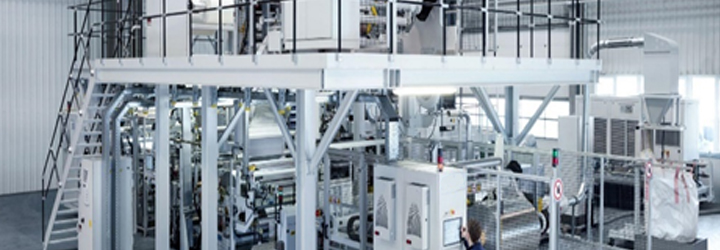